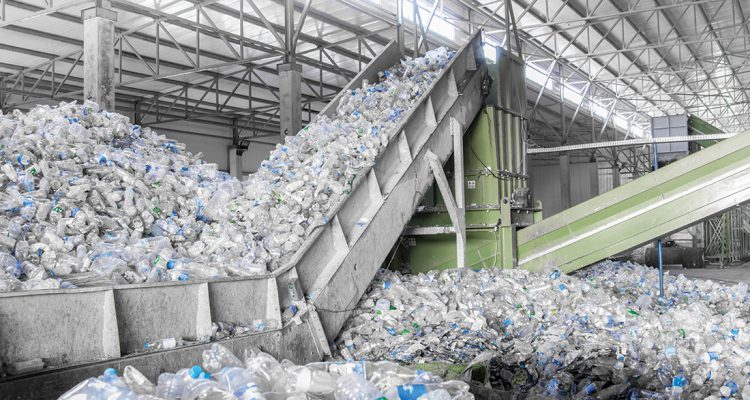
13 Mar Giving waste management inefficiencies a good belting
The foundation of efficient waste management comes down to the wrapped belts that keep the machinery rolling. Compared with other developed economies, Australia generates more waste than average and recycles less. Since the Australian Commonwealth appointed a Minister for Waste last year, the nation’s effort in recovering waste has been improved.
The national packaging targets aim to ensure 70 per cent of all plastic packaging is recycled by 2025 and resource recovery facility operators are being encouraged to assist with significant environmental outcomes as the sector continues to see growth in economic opportunity and increased material availability.
Recycling plant operators have five years until the 2025 National Packaging Targets deadline approaches to capitalise on expected throughput growth. As recycling demands increase, streamlining equipment processes through installation of durable belt drives will be a key investment for recycling plant operators to reach the ultimate high-level of efficiency.
This can be achieved for recycling plant operators by installing Carlisle belts. In order to maintain operations and minimise downtime, wrapped v-belts become a critical component in the facility’s procedure.
BSC prides itself on being innovative in waste management. Providing a diverse range of belt drives to facilitate recycling applications has proven to be a performance enhancing tool for companies across the country. Companies rely on the efficient operation of their equipment that is driven by market leading belts with an electric motor, as it ensures the smooth operation of sorters, conveyors and crushers involved in the collaborative recycling process.
To provide a complete power transmission package, BSC works closely with the American manufacturer of Carlisle belts by Timken. For over 100 years, Carlisle belts have been manufactured in the US. The Timken Company acquired Carlisle belts in 2015.
Backed by a long history in serving recycling plant operators and assisting ultimate waste management, new belt lines and products to the market, has prepared customers for the changes happening across the industry as the nation strives towards a new level of stream-lined recycling ahead of the 2025 packaging targets.
Carlisle belts by Timken are supplied exclusively to BSC as part of Inenco Industrial Solutions. Steve Hittmann, National Product Manager at BSC says every belt is backed by extraordinary engineering and technical support from BSC’s product specialists and engineered services team.
“And combining that with the Carlisle factory back-up, our personal, knowledgeable, and attentive customer service team are second to none,” he enthuses.
As operations ramp up across national recycling plant facilities, Steve says it’s more important than ever to have on-time delivery and fast turnaround. Combining BSC’s distribution and Carlisle’s flexible manufacturing model, customers in the waste management sector are experiencing short lead times and reliable delivery that are exceeding their expectations and outlasting competitors’ belts.
Steve says the Carlisle Blue Label V-belts are the finest wrapped belt in the industry.
“They’re a classical V-belt work-horse,” he says. “They also assure dependable length stability and require less re-tensioning and take-up.”
Steve adds that due to the daily operational demands at recycling plants, having wrapped belts that resist flex fatigue and have a proven longer belt life will ensure smoother waste management.
“The Carlisle Blue Label V-belts have proven to be an efficient tool as the cord is coated with a special compound that produces a secure, long-lasting bond with surrounding rubber,” he explains. “Longer belt life results in less frequent replacement, less downtime and lower maintenance costs,” Steve says.
In recycling plants, there are a lot of extremely heavy, awkwardly shaped products moving around at a high velocity. The heavy-duty fabric cover protects the core but also its extra flexibility permits the belt to bend more easily around the smallest pulleys with less strain on the fabric, which achieves the perfect amount of slip and grip needed to put the rollers in motion.
Enabling a better flow of product through the plant relies on belt drive construction and design, as that can influence overall lifespan, power transmission and efficiency. Carlisle belts are specifically designed for the harsh environments of resource recovery.
BSC and Carlisle belts by Timken have extensive experience working with numerous companies in the waste management industry across Australia and their experience enables them to understand and grow businesses through energy conservation, high sustained speeds and continuous production as the entire sector undergoes a market changing recycling revolution.